|
|
汽车工业
- Automotive Industry
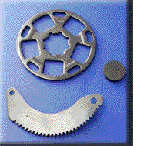
亲爱的访问者,
在您探访本站之前, 请注意该部分网页内容正在建造中.
对由此引起您的不便我们真诚表达歉意.
请在英文网页继续您的浏览. 如果无法找到您需要的信息请与我们联系.
Computer-regulated
nitriding has made great headway in the automotive branch often replacing
traditional gas nitriding, salt bath and ion (also known as plasma) nitriding,
as well as carburizing. A number of automotive manufacturers are specifying
surface properties that would be difficult or impossible to achieve without the
use of controlled nitriding methods. Besides, close tolerances specified for a
number of critical components call for, among other factors, close temperature
control. The Nitrex series of nitriding furnaces is capable of achieving
temperature uniformity within ± 3° C throughout the retort.
Comparison table shows the advantages and disadvantages of different nitriding
methods currently employed.
Nitriding properties required:
Wear resistance, anti-seizure properties, corrosion resistance, fatigue
resistance.
Case study:
In non-alloyed steels and cast irons, Nitreg® nitriding produces practically
only a compound layer composed of g‘
or e+g‘
nitrides. The surface hardness is not very high (HV1 = 320 - 380 for mild steel,
400 - 580 for cast iron), but sufficient to improve wear resistance
considerably. At the same time, in conditions of insufficient lubrication, the
resistance to galling, or seizure, is strongly improved. A typical example is a
clutch hub made of low carbon steel. The requirement is a 6 µm minimum compound
layer, and passing a specified long-term wear test. In the first approach, by
one supplier, plasma nitriding was employed. However, the required case depth
uniformity over the whole profile of the spline teeth could not be met. Nitreg®
proved to be superior with respect to white layer requirements and the layer
itself was found to be more uniform, especially in the fillets. After the test
involving 1500 load cycles, the Nitreg® nitrided surface was still free of any
signs of wear.
List of applications

后退
顶部
|